GEN II Round Planar Magnetron Sputtering Sources
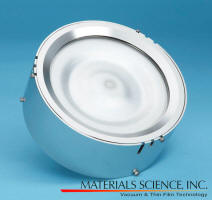
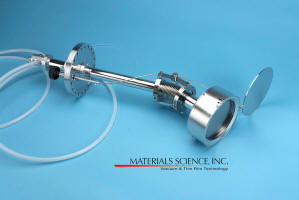
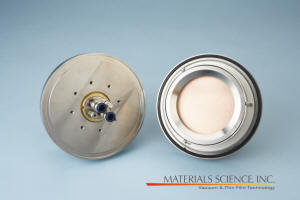
Typical GEN II Internal Mount Configuration Typical GEN II Adjustable Internal Mount with Tilt & Shutter on CF Flange Typical GEN II Flange Mount Configuration SunSource™ Round Planar Magnetron Sputtering Source Sales Brochure: MC 310 5/12
Key Features - Wide Uniform Erosion Area results in stable operation, minimal distribution & uniformity/rate changes throughout the target lifetime.
- Active Plasma Discharge on nearly entire target surface keeps target clean & reduces insulating film growth that leads to arcing.
- Argon Gas Through Cathode Body - Additional Feedthroughs, external manifolds & other plasma disturbing hardware that increases required periodic maintenance frequency is unnecessary.
- Modular Design - Tilt, Adjustable Height and Position, Shutter Mechanism and Mounting Flange/Feedthrough easily configured and added to using industry standard fittings and components. User friendly and serviceable.
- Available in 4" to 8" Diameter Targets
- Internal and Flange Mount Configurations
- Can be Used in DC, Pulsed DC, AC, RF & HIPIMS Modes
- 35-40 Wt% Target Utilization in real life operation (highest available)
- Low 10-4 Torr Operation
- Fully Stoichiometeric Dielectric Materials at Low Pressures & Temperatures
- 20% Higher rates due to broad erosion area & highly efficient cooling.
- Mechanically Robust and Reliable - NO Screw insulators, Very high dielectric value Ultem instead or Delrin or Teflon insulators, stainless steel water tubes with push-to-connect, no flow restriction unions, larger diameter fasteners with course threads and permanent i-Kote™ no galling/anti-seizure coatings. NO tapped holes in cathode body for target clamp fasteners to seize in or back out helicoil or other inserts.
|
Basic Sputter Source (click on photographs to enlarge)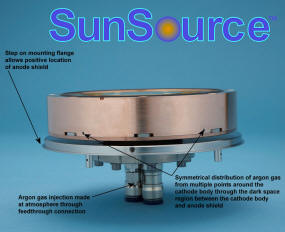 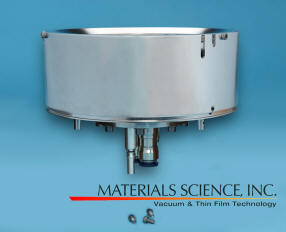
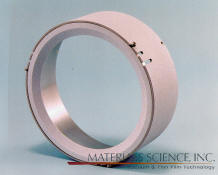 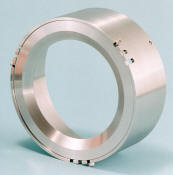
Optional Thermal Sprayed Anode Shields greatly Standard anode shields are electropolished reduce flaking and particulate generation. 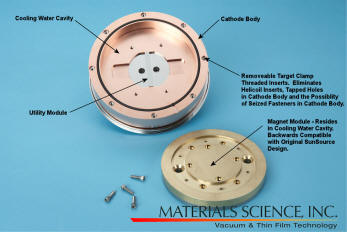
High Reliabiilty - Low Cost of Ownership 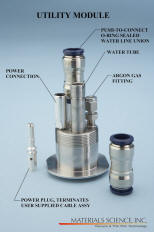
Power, water & gas connections are made on the utility module. Push to connect water fittings eliminate leakage common with compression fittings. The module can be easily replaced by the user if any of the utility connections are damaged beyond repair or replacement. The need for a separate argon gas line and manifold is eliminated. No water flow restrictions within the cathode body or through the water fittings. The clear ID of the water tubing and it's length is the only restriction on flow. Water flow rates through SunSource GEN II™ sputtering sources can be nearly twice as high as competing sources. 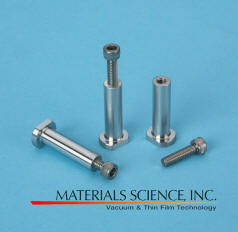
i-Kote™ adaptive coating on target clamping ring and anode shield fasteners virtually eliminates galling and seizure of screws. Unlike silver plating and other coatings, fasteners with the i-Kote™ coating may be re-used many times.
Experienced users know that Helicoil™ and other threaded inserts often are backed out of the cathode body when fastener galling occurs. Worse yet, the screw often seizes in the cathode body, requiring it to be drilled out and the body re-machined. The combination of the proprietary, easily removable cathode body target clamp threaded inserts and the i-Kote™ coating on the screws very significantly reduces cost of ownership and vastly improves uptime. Simply cut of either the flange on the insert or cut/break off the screw head, and replace them with inexpensive parts on-site. Access to a machine shop is not necessary.
Water, power & gas connections made at atmosphere 4 threaded vented mounting points are provided through bulkhead KF-50 flange on Internal Mount Sources Summary of Operational/Maintenance Benefits Compared to Competing Sources - Highest quality, not cheapest construction. Built to last.
- No screw insulators - less frequent maintenance and lower costs
- Very high dielectric strength insulators - withstands "ringing" of commercially available AC power supplies
- No threaded "adjustable" anode shield - this just galls nearly immediately
- Unrestricted water flow through sputtering source
- Seizure of target clamp screws virtually eliminated
- Target clamps, shields and cathode body are not sputtered - they are not consumable items
|
Process Benefits Better Distribution Uniformity Control of pressure and flow on the target surface made possible by argon gas injection through the cathode body enables a stable plasma discharge and uniform sputtering conditions. Process asymmetries caused by poor pumping and flow conditions within the vacuum system are minimized. |
Longer Useful Target Life The profile of the eroded area remains relatively constant and does not begin to dramatically pinch as he target is consumed causing radical changes in the uniformity of the deposited films. Premature target burn-through resulting from venturi effects on the target caused by the use of gas fittings on the ground shield or separate "chimney" is avoided due to argon gas injection through the cathode body. |
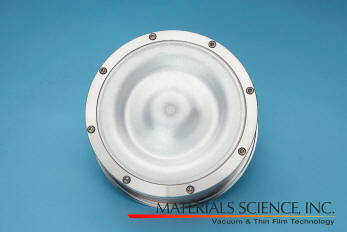
Argon gas flows symmetrically through the cathode body and uniformly across the target surface, eliminating localized high pressure regions on the target surface. Premature target burn-through and skewed distribution are prevented. Argon gas flowing from the target surface creates a localized high pressure which reduces the tendency of sputtered material to redeposit on the target surface Ideal for Reactively Deposited Films The broad plasma discharge minimizes insulating film growth on the target surface which causes arcing. It also reduces redeposition of back-scattered material on the target in non-active areas. This is especially important when the redeposited material is highly stressed and likely to fracture, resulting in particulate generation and film defects. The efficient thermal design of SunSource™ sputtering sources lowers the tendency toward insulating nodular and whisker growth caused by hot spots on the target surface because the entire target assembly is uniformly cooled. | 20% Higher Rate of Deposition Compared to Competing Designs More power can be applied to the target without negative side effects such as magnet degaussing and target overheating. The 6" round SunSource™ sputtering source has a 1 gpm higher flow rate compared to the next best competing product (5 gpm vs. 4 gpm at the same inlet and outlet pressures), resulting in 20% higher rates. The 4" round SunSource™ sputtering source can be run at continuous power levels of 7 kW (nominal 560 watts/in2) at 3 gpm compared to the next best competing source which has a maximum flow rate of 2 gpm at twice the inlet pressure. |
Modular Design - Easy and Inexpensive to Configure When Ordering or in the Future - Simple & Cheap Maintenance 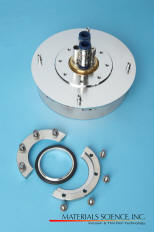
The KF-50 bulkhead flange on the basic sputtering source allows the connection of a wide variety of feedthrough possibilities, including adjustable height, tilt, X-Y-Z positioning and shutter mechanisms. ISO, ASA and CF flanges can be added with the appropriate compression or other fitting welded to the flange. A few examples follow. 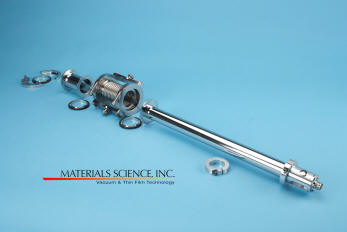
Adjustable height feedthrough with tilt mechanism. Both are options. Standard hydroformed bellows can be obtained from a multitude of standard component suppliers overnight, worldwide. The bellows is not welded to the either the feedthrough or the sputtering source assembly. It's not necessary to have access to a machine shop and welding capability to replace a failed bellows. 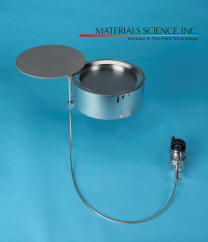
Typical shutter assembly, with flexible cable allowing easy installation of shutter mechanism in existing systems It's another option. Lightweight titanium shutter has a textured surface to minimize flaking and maximize material adhesion.
Shutter is mounted on top of KF-50 bulkhead clamps on basic sputtering source. This allows anode shields to be cleaned simply and easily. Shutter is not mounted or welded to the side shield as is the case in competing designs. Ferrofluidic rotary feedthrough is provided - can be 1" baseplate feedthrough or 1.33" or 2.75" CF flange mounted version.
Manual, pneumatic or electropneumatic versions can be provided. 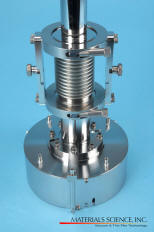
Adjustable height, tilt and shutter mechanism installed on basic SunSource™ sputtering source. Shutter not installed. 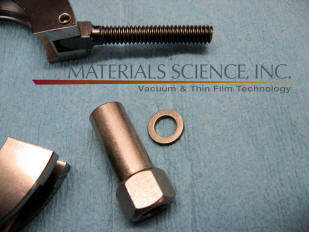
Adaptive i-Kote™ coating is applied to threads on KF-50 stainless steel swing clamp that is part of tilt mechanism. Screws on assembly also have the coating applied. 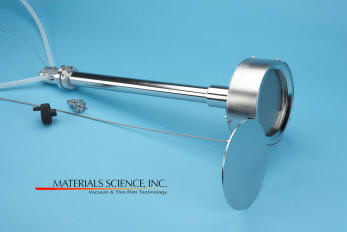
Shutter mechanism with flexible cable and ferrofluidic rotary feedthrough 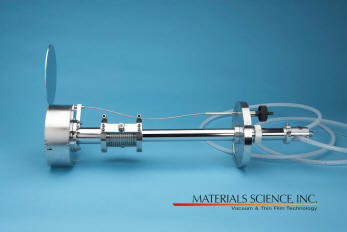
SunSource GEN II™ with adjustable height feedthrough, tilt mechanism, manual shutter - mounted on 8" OD CF flange Application Examples 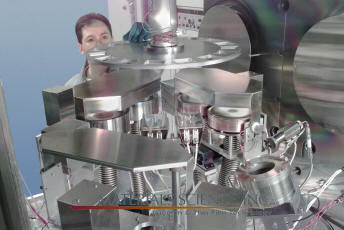
Ion-assisted reactive sputtering system for DWDM filters |